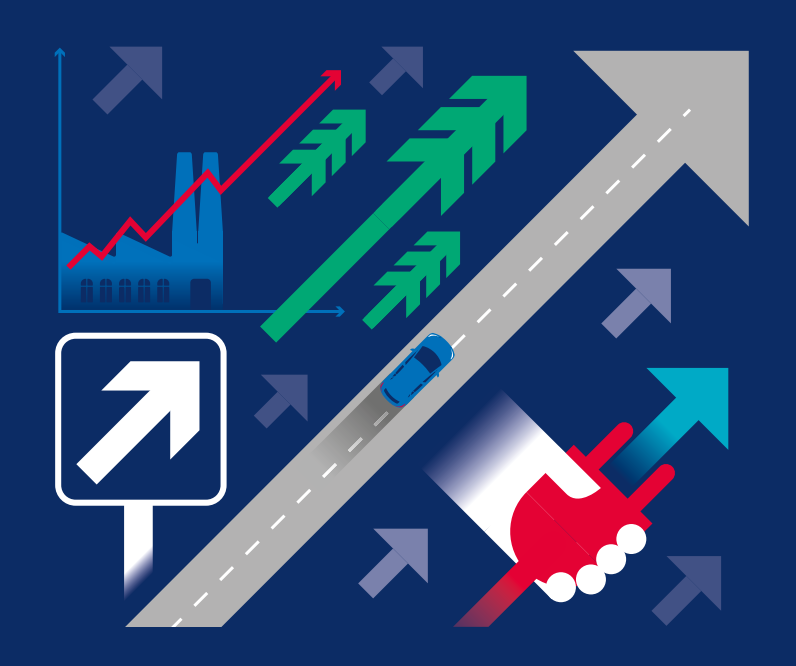
Leading net-zero, supporting high-value, rewarding jobs, delivering for the economy, producing cutting-edge technology, and driving exports and growth – a strong domestic automotive sector is rightfully an ambition of all nations.
The UK’s automotive industry is one of its most valuable assets and it is one of the world’s most diverse, manufacturing cars, commercial vehicles, buses, engines, parts and components, as well as a thriving aftermarket and one of the most vibrant and progressive markets, seeking to lead on technological change.
From Full Throttle to Full Charge marks the next stage on the UK’s journey to Net Zero, presenting an updated roadmap and new forensic analysis of the supply chain that is necessary if we are to ensure UK Automotive is competitive at home and abroad.
Full Throttle was published in June 2021, emerging from lockdowns towards what was hoped was going to be a period of economic recovery and growing confidence in industry’s ability to deliver on shared goals – if the right conditions were put in place. Fast forward just 12 months and the operating landscape has changed dramatically and unexpectedly.
A Covid resurgence; war in Ukraine; volatile energy markets; soaring commodity prices; a cost of living crisis; spiralling inflation; component shortages; supply chain disruption; logistics upheaval; trade uncertainty; regulatory change; and a climate emergency. Each a challenge to growth of itself but, collectively, the most significant storm to beset the industry in a generation. All at a time when the industry is facing the most radical technological change since its inception.

Automotive is global and the UK industry is not alone in its ambition, its transition or its challenges. But the UK has additional issues with which it must deal: changing trade relationships, markedly higher energy costs and the most ambitious timescale for regulatory measures to deliver zero emission mobility.
The race is on. We must create the most competitive conditions for investment; to build battery production and electrify supply chains; to upskill our globally renown workforce to ensure they are fit for the future; and to help our existing manufacturing base grow and prosper in the electrified age.

We recognise the competing pressures on Government and UK spending. However, the strategic importance of automotive should not be ignored. We need to build confidence, consistency and competitiveness. Action now will drive economic growth in the years to come. With the right support on business costs; on supply chain security; on skills; innovation and investment, our industry can repay investment many times over and not just recover but thrive in the global economy.
The prize is significant: accelerated decarbonisation will help the UK meet carbon budgets; a healthy market will afford consumers choice and increasing affordability to make the leap into new technologies; creating competitive conditions for our world-leading manufacturing capabilities will provide exports leadership; and investment into our people will support households and economies across the entirety of the UK.
This can only happen if all stakeholders work together. From Full Throttle to Full Charge provides a deeper understanding and consolidated policy roadmap to better illuminate the way.

