Supporting Sustainability
UK automotive companies specialising in manufacturing, remanufacturing, supply chain, logistics, R&D and aftermarket have a clear, ongoing commitment to improve their social, environmental and economic sustainability.
Delivering Sustainable Growth
For the automotive industry, ‘sustainability’ is more than simply tailpipe emissions, it’s about championing new strategies and technologies that make producing, maintaining and using vehicles even better for people and the planet.
Over the past 25 years, the industry has made tremendous progress, halving average CO2 emissions per vehicle produced and reducing manufacturing waste to landfill by -99%. Use of water and volatile organic compounds are down -42% and 55% respectively, while lost time incidents are -91% lower.
With the right support and strategic approach, the transition to a net zero and circular economy will create new opportunities and provide the UK with a competitive advantage.
SMMT campaigns for:
- A green automotive transformation strategy that sets out a holistic, joined-up approach and provides a pathway towards the UK automotive industry’s ultimate sustainability and circularity goals
- Support and guidance to empower a sustainable, transparent UK supply chain
- Fiscal, tax and regulatory support measures that attract new investment and ensure domestic vehicle producers are globally competitive
- A skilled, diverse, empowered UK workforce
- A UK regulatory ecosystem in partnership with business that is ambitious, deliverable and harmonised with global regulatory requirements and international sustainability objectives
- Ensuring UK sustainability data requirements match the high ambitions of automotive companies operating across global markets
- Maintaining and further supporting access to critical raw materials and cross-border trade, building supply chain resilience to attract investment in zero emission and sustainability technologies
Automotive sustainability covers the gamut of operations, including:
- Vehicle Emissions and Air quality
- Resource usage, waste and recycling
- Ethical supply chains
- Health & safety, training and apprenticeships, and diverse, equitable workforces
SMMT 25th Automotive Sustainability Report
Over the last quarter of a century, the sustainability landscape has transformed. The UK Climate Change Act has created a legally binding commitment for UK government to deliver the Paris Climate Change Goals and achieve net zero by 2050 – and the automotive industry has long-recognised its critical role in meeting this target.
The industry’s commitment and progress is covered by the annual SMMT Sustainability Report, published every year since 2000. The report provides a comprehensive overview of the industry’s sustainability performance, across environmental, social and business terms.
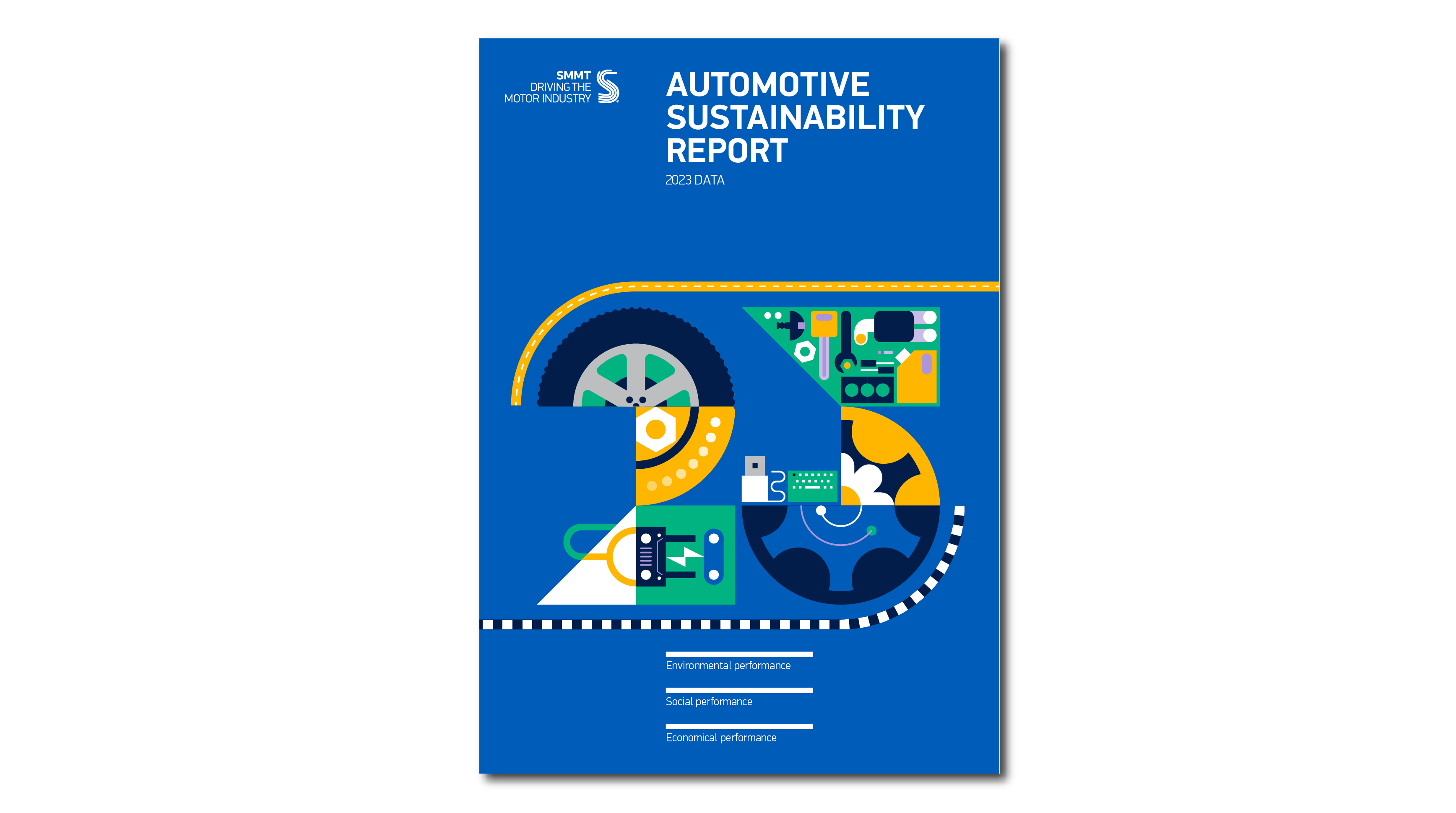
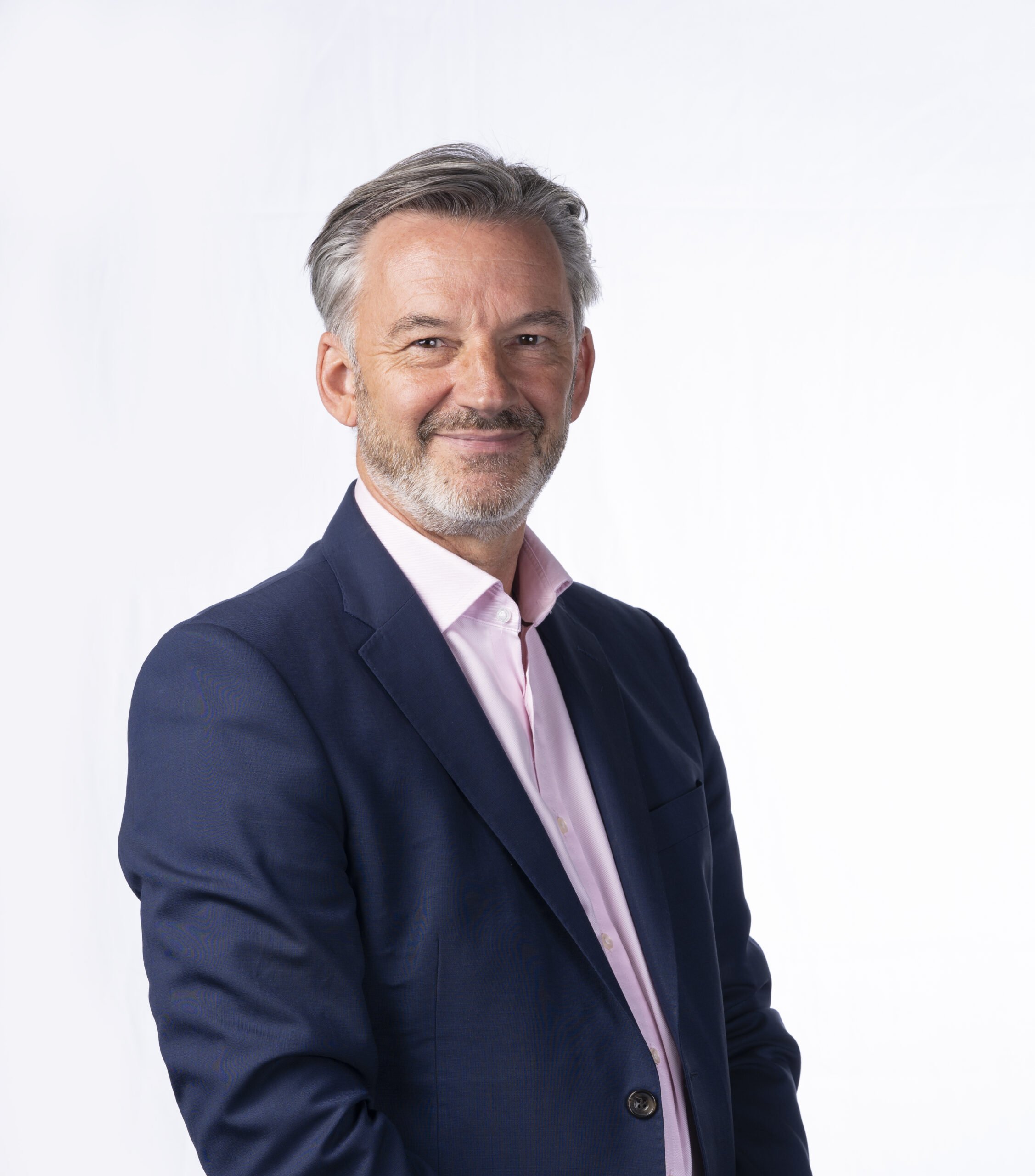
“Britain’s automotive sector has been cutting carbon for decades and this new milestone is significant, not just for industry but for the nation’s move to net zero. We look forward to working with the new government to deliver its green growth agenda that puts Britain at the front of the queue for global investment and sustainability leadership. Automotive can be the driving force behind this strategy, reducing carbon emissions still further while growing the economy, improving air quality and delivering new jobs and skills for people across the country.”
Mike Hawes, SMMT Chief Executive
Key Sustainability Data
Sustainability summary since 1999
-55%
Total Scope 1 & 2 energy down
-91%
Lost time incidents down
-53%
VOC emissions down
-33%
Scope 1 & 2 energy per vehicle down
-42%
Water per vehicle down
-54%
CO2 per vehicle down
-99%
Manufacturing waste to landfill down
-78%
Exhaust emission NO2 down
-89%
Exhaust emission particulates down
The automotive industry is committed to cutting tailpipe emissions – helping reduce the impact on climate change, but also on air quality.
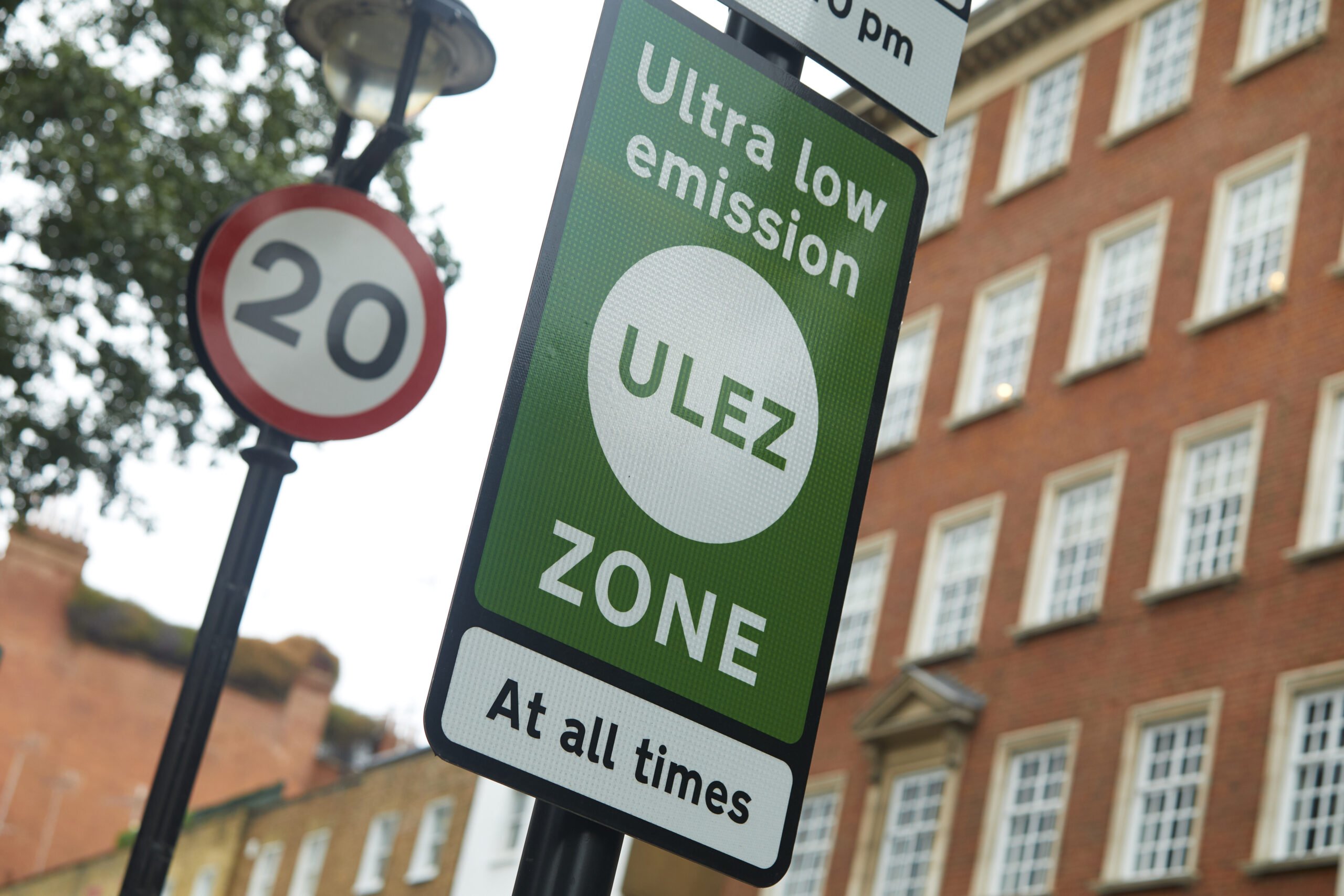
The safety of all road users is a high priority to all manufacturers in the motor industry. Implementation of new technological developments ensures that improvements in occupant and pedestrian safety continue to be made.
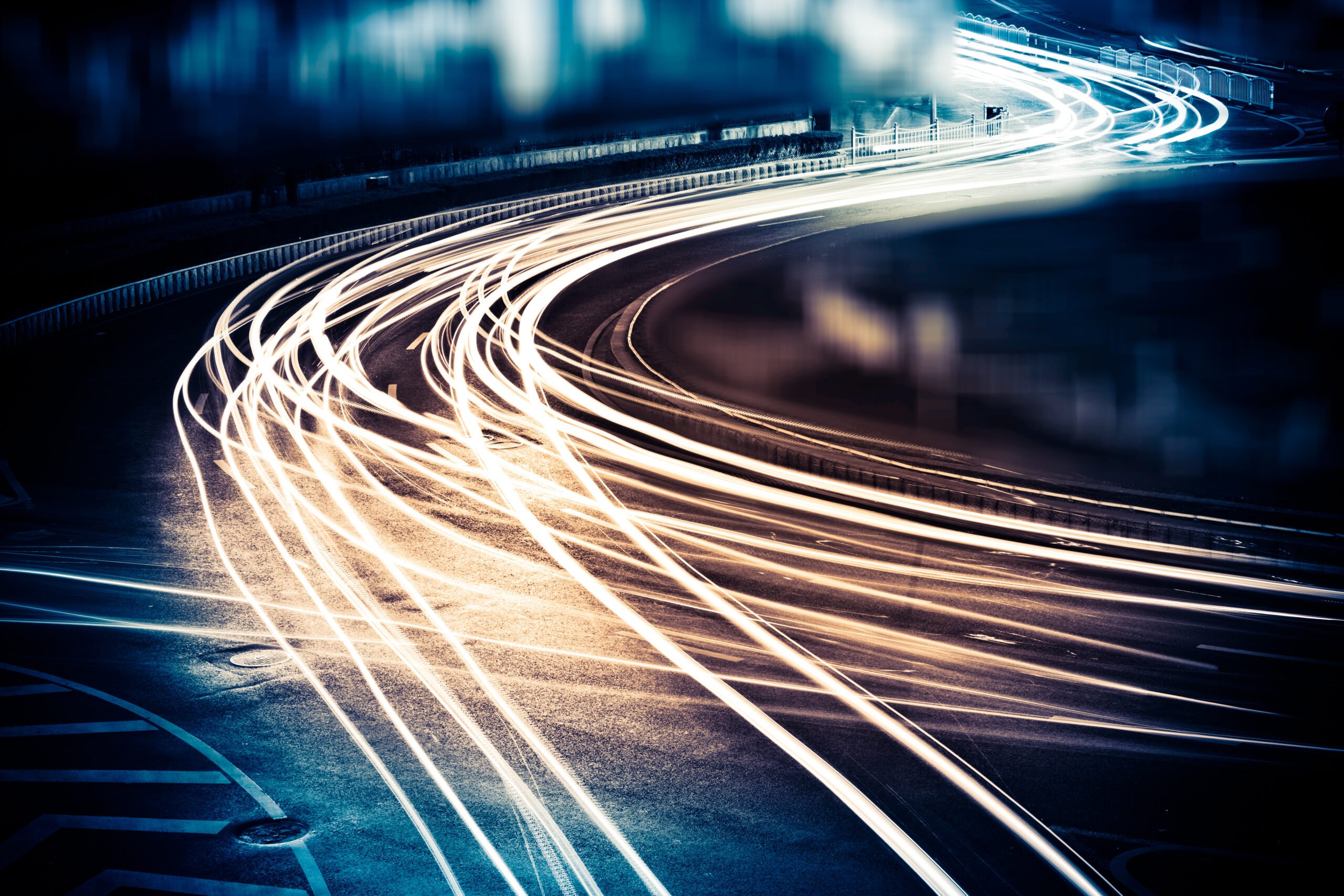
REACH came into force in June 2007. It aims to reduce the risk from chemicals to humans and the environment and encourages the substitution of unsafe chemicals. The rules affect manufacturers and suppliers in the automotive industry and also companies in other industry sectors.
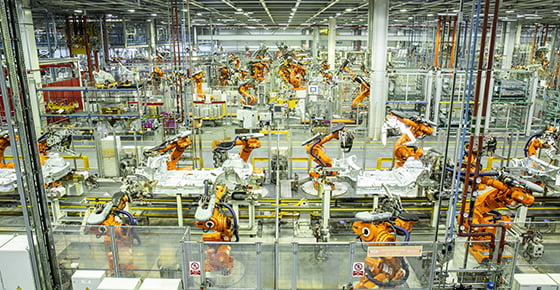
The automotive industry is one of the world’s most prolific recyclers, recovering metals and non-metallic parts from vehicles that have reached the end of their use to build the next generation of cars, vans, trucks and buses.

Energy efficiency support
The automotive industry is committed to cutting carbon at every stage – including manufacturing. A significant part of that is improving energy efficiency.
The industry is covered by several energy efficiency regimes, including:
- UK Emissions Trading Scheme (UK ETS)
- UK Climate Change Agreements (CCAs)
- Energy Savings Opportunity Scheme (ESOS)
- Simplified Energy & Carbon Reporting (SECR) rules.
UK ETS
The UK Energy Trading Scheme sets caps on the amount of permitted emissions. Participants can comply with the scheme through trading allowances.
The scheme covers gas use in electricity generation, the main energy intensive industries and the manufacture of vehicles. SMMT members are covered through combustion activities, such as gas use in boilers and heating systems.
CCAs
SMMT operates a Climate Change Agreement on behalf of its members, which provides the opportunity to save 92% on the Climate Change Levy on electricity, and 89% on gas.
The discount depends on fulfilling a contract which includes energy efficiency targets.
Eligible energy use would be for activities such as:
- Body pre-treatment and paint processes
- Boilers and heating systems with aggregate capacity over 50 MW (also CHP)
- Effluent treatment plant
- Press shop
- Foundries for casting components
- Lighting, heating, ventilation, compressed air, etc. to support the above.
- Some heat treatment processes related to energy intensive activities
Ethical supply chains
The industry is committed to sourcing raw materials for production in an ethical way that has a positive impact on communities around the world.
Many manufacturers are members of the Drive Sustainability initiative, working together to improve the social, ethical, and environmental performance of automotive supply chains.
Diversity, Equity and Inclusion
Signatories to the Automotive Council’s Diversity Equity and Inclusion Charter have pledged to increase the female proportion of their workforce to 30% by 2030, compared with today’s industry average of 14%.
The industry also invests heavily in training the next generation of top talent from as broad a section of society as possible. The number of apprenticeship and trainee starts increased by more than 40% in both 2022 and 2023, demonstrating the sector’s commitment to build a sustainable, inclusive succession pipeline.
Automotive Insights
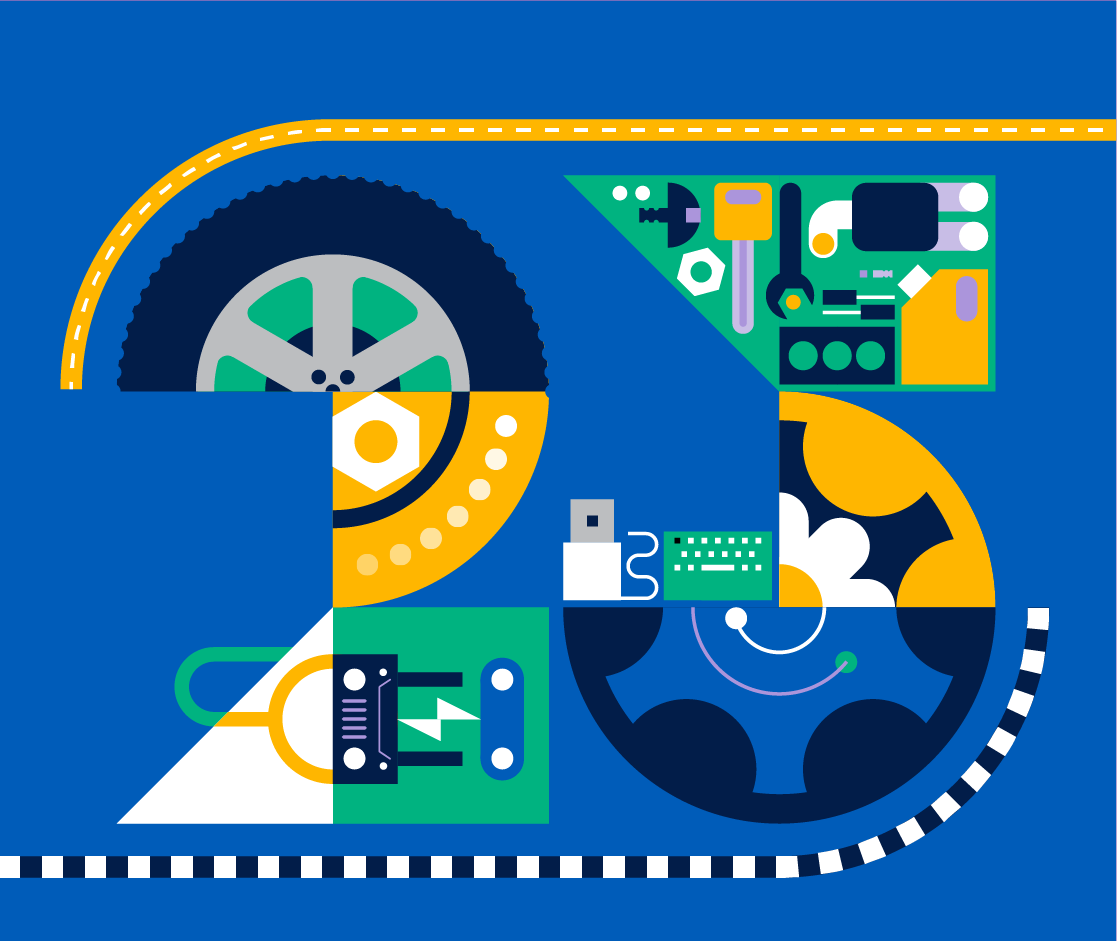
UK Automotive Sustainability Report
A quarter of a century ago, the UK automotive industry made clear its commitment to sustainability with the publication of SMMT’s first annual sustainability report. As consecutive reports over the following 25…
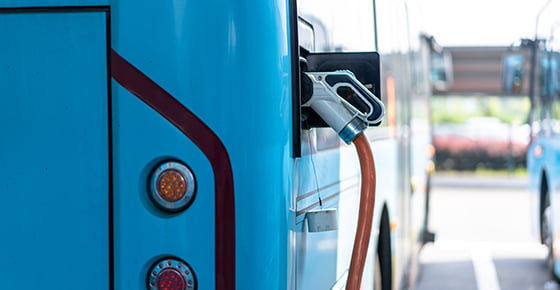
Britain’s buses need a timetable to arrive at Net Zero
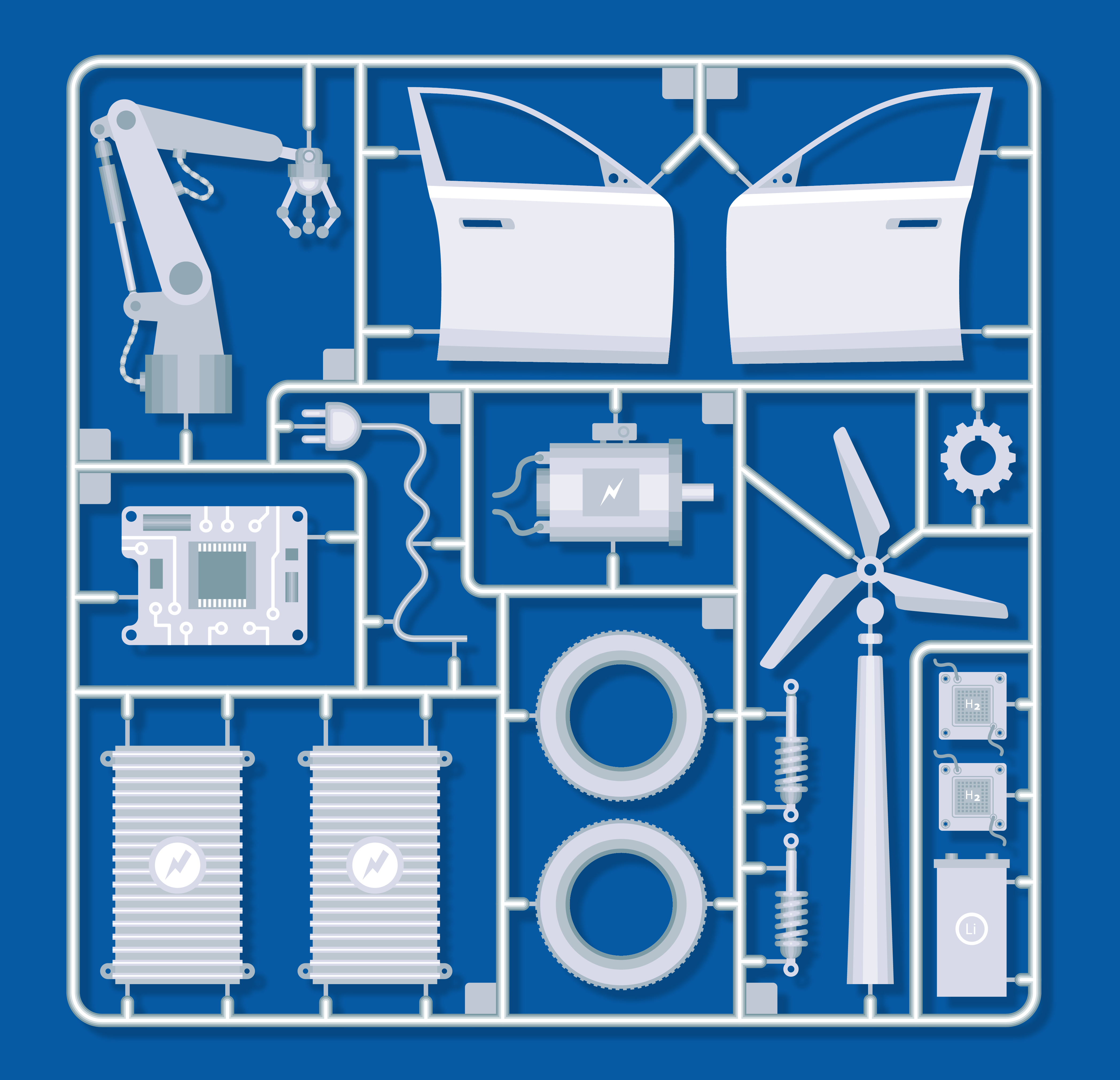
Race to Zero: Powering Up Britain’s EV Supply Chain
apply to join
SMMT’s comprehensive membership base covers every aspect of the automotive industry, from vehicles to components, trailers to aftermarket; and from large global corporations to small and medium enterprises. The scope of interest of our members also varies dramatically, ranging from direct, partial or indirect involvement in the manufacturing of vehicles and components, to design engineering and distribution, and a variety of other services aligned to the industry.
Get in touch to find out how to join SMMT.
If you are already a part of an organisation that has an SMMT membership, click here to register your account.
Find out how your company can become a member of SMMT.
"*" indicates required fields