media centre
Keep up to date with the latest news, comment and insight from SMMT, covering all key UK automotive industry issues, developments and trends, including market and manufacturing performance across every sector.
News
FILTER search:
Select year
Select year
2025
2024
2023
2022
2021
2020
2019
2018
2017
2015
2014
2013
2012
2011
2010
2009
2008
2007
2005
2004
2003
2002
2001
2000
1999
1998
1997
1995
1994
1993
1992
1991
1990
1989
1988
1987
1985
1984
1983
1982
1981
1980
1979
1978
1977
Select month
Select month
Jan
Feb
Mar
Apr
May
Jun
Jul
Aug
Sep
Oct
Nov
Dec
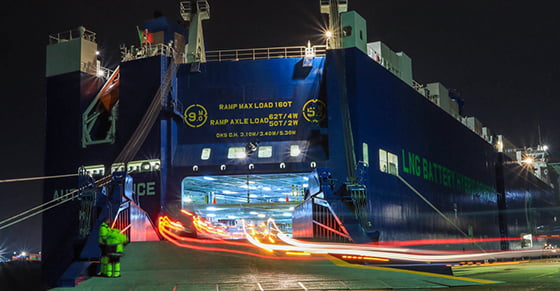
News
CEO Update
UK deal remains America’s first – and so far only – automotive trade deal
4 Jul 2025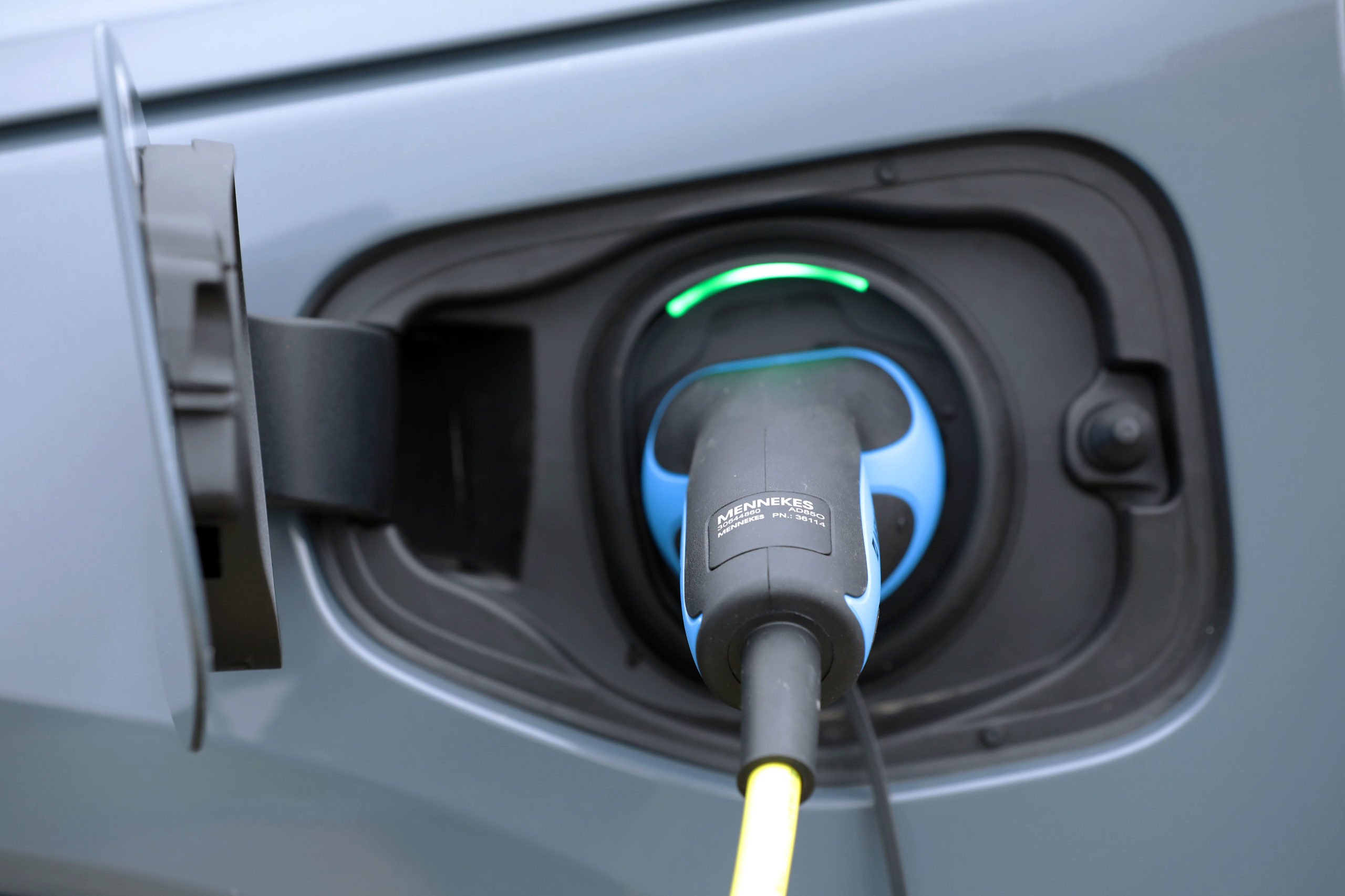
News
Commercial Vehicle
LCV registrations
Van market down every month in first half of 2025
4 Jul 2025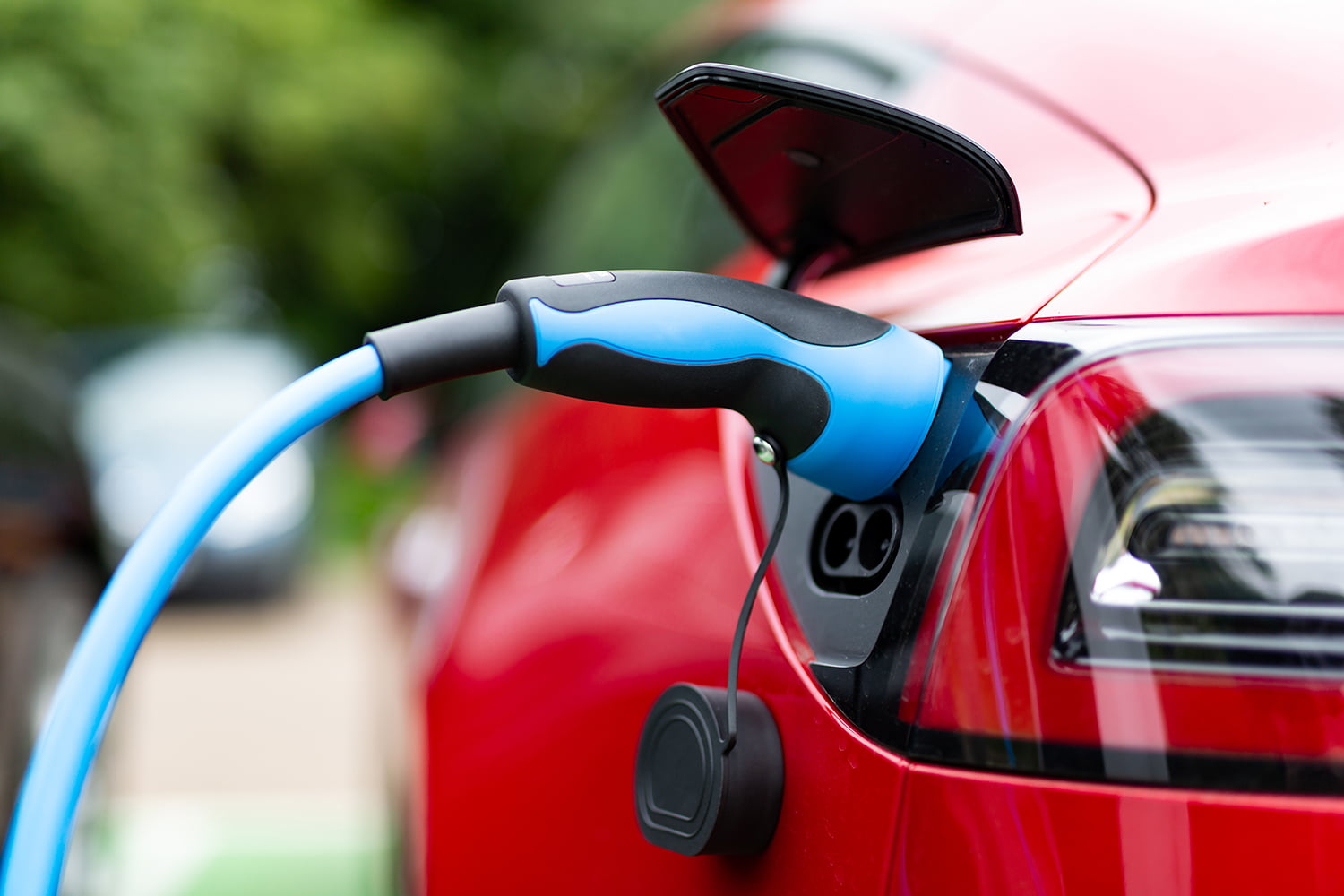
News
Car
Car registrations
Bumper June for UK new car market as one in four buyers goes electric
4 Jul 2025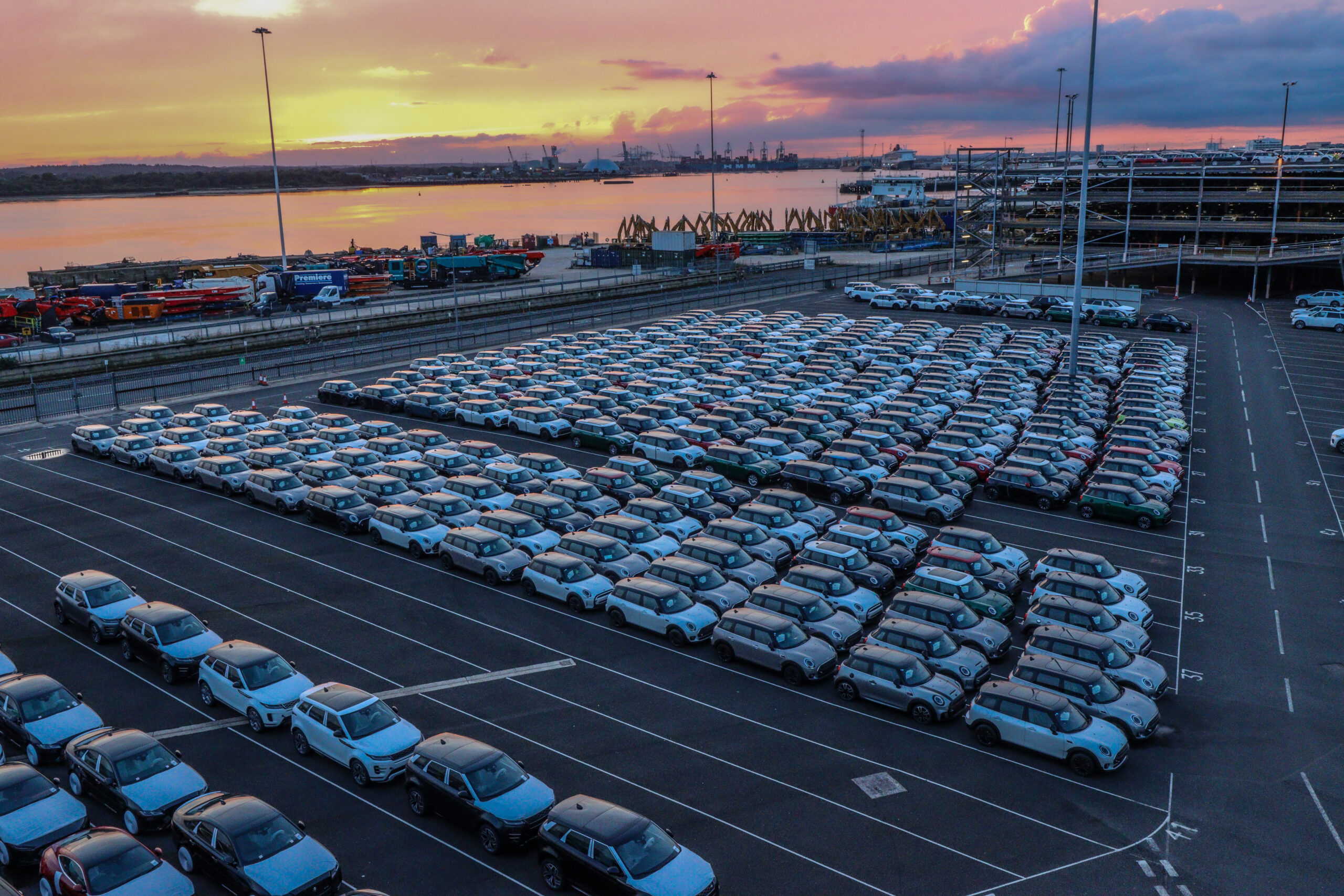
News
Trade
SMMT statement on UK-US trade deal kicking into gear
30 Jun 2025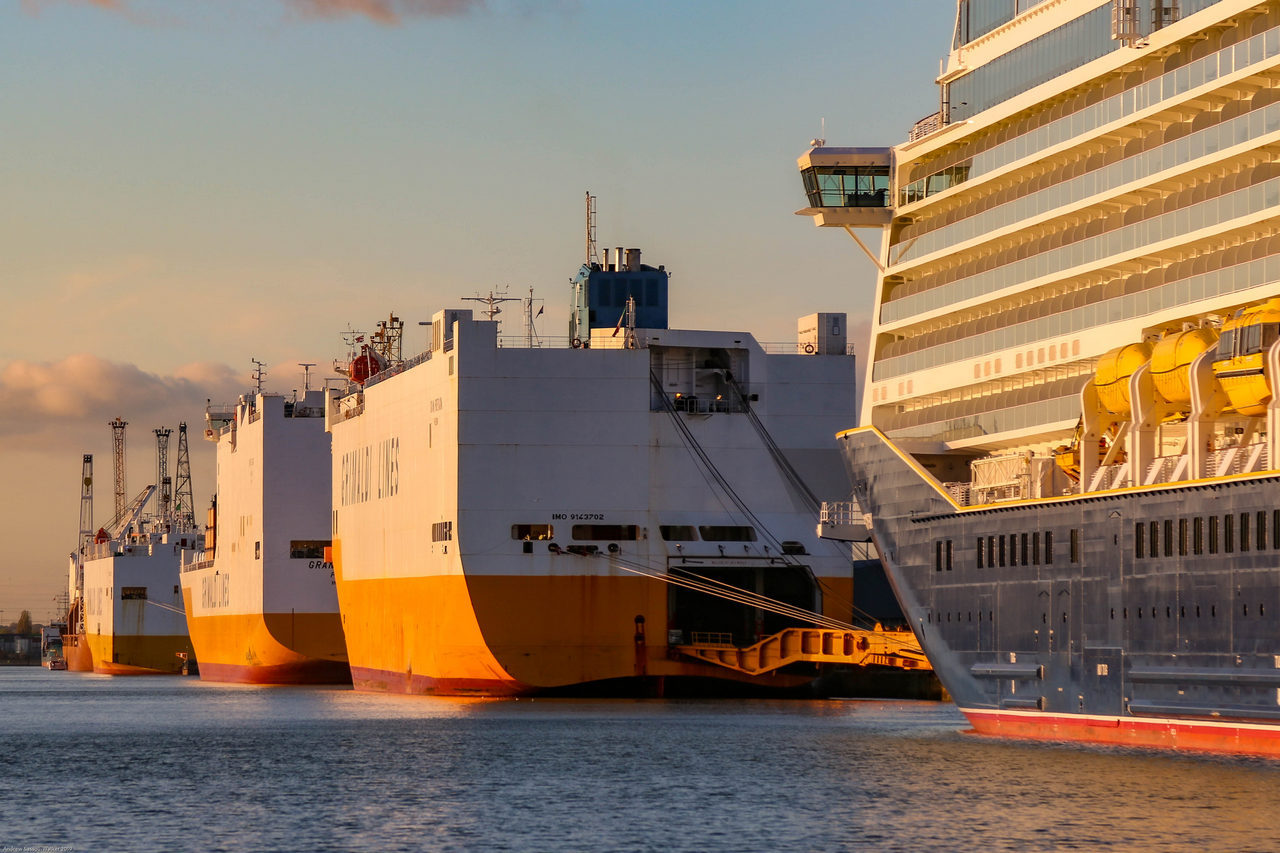
News
CEO Update
A landmark week for UK industry
27 Jun 2025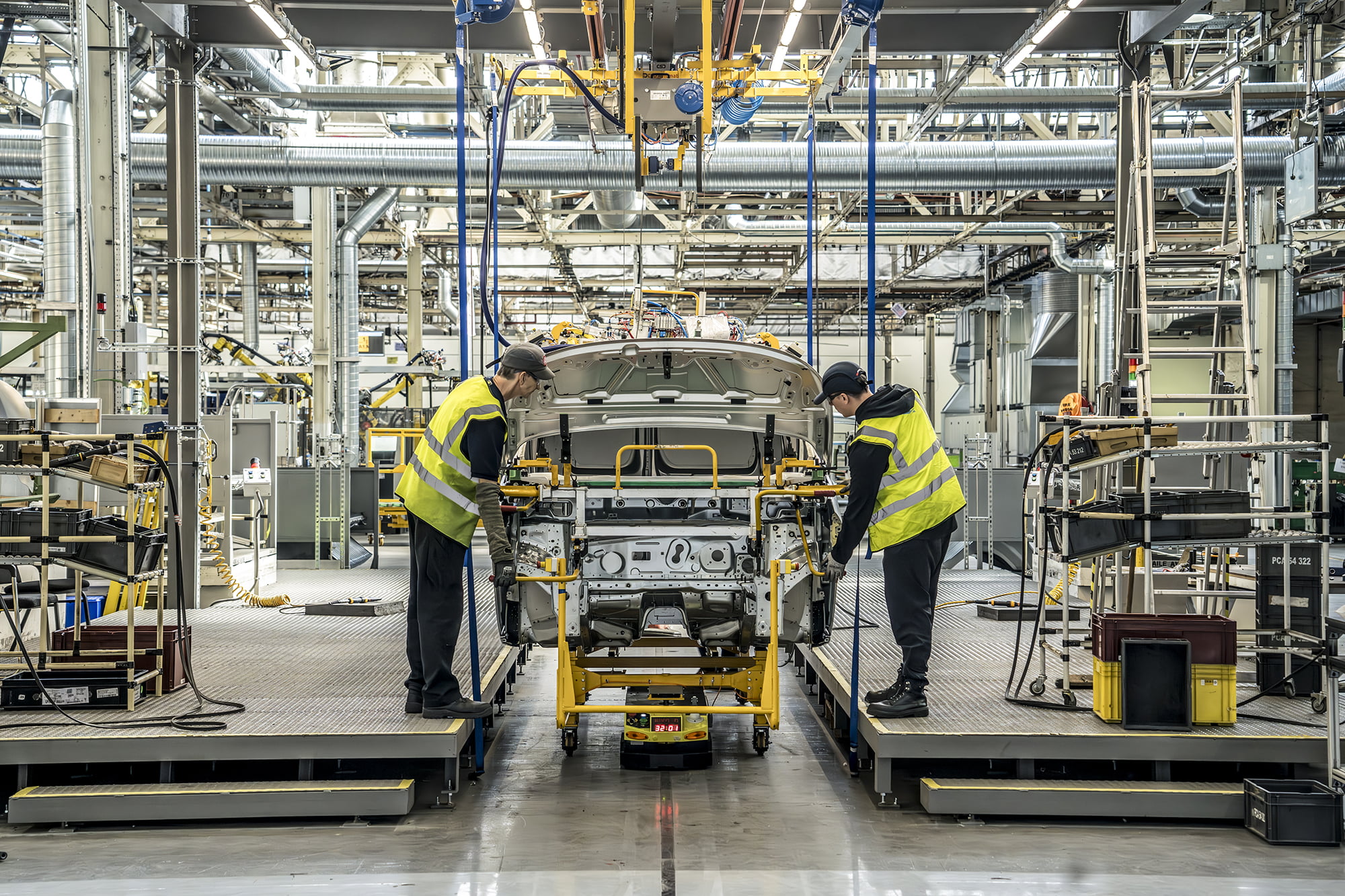
News
Car
Car manufacturing
UK vehicle production constraints continue in May
27 Jun 2025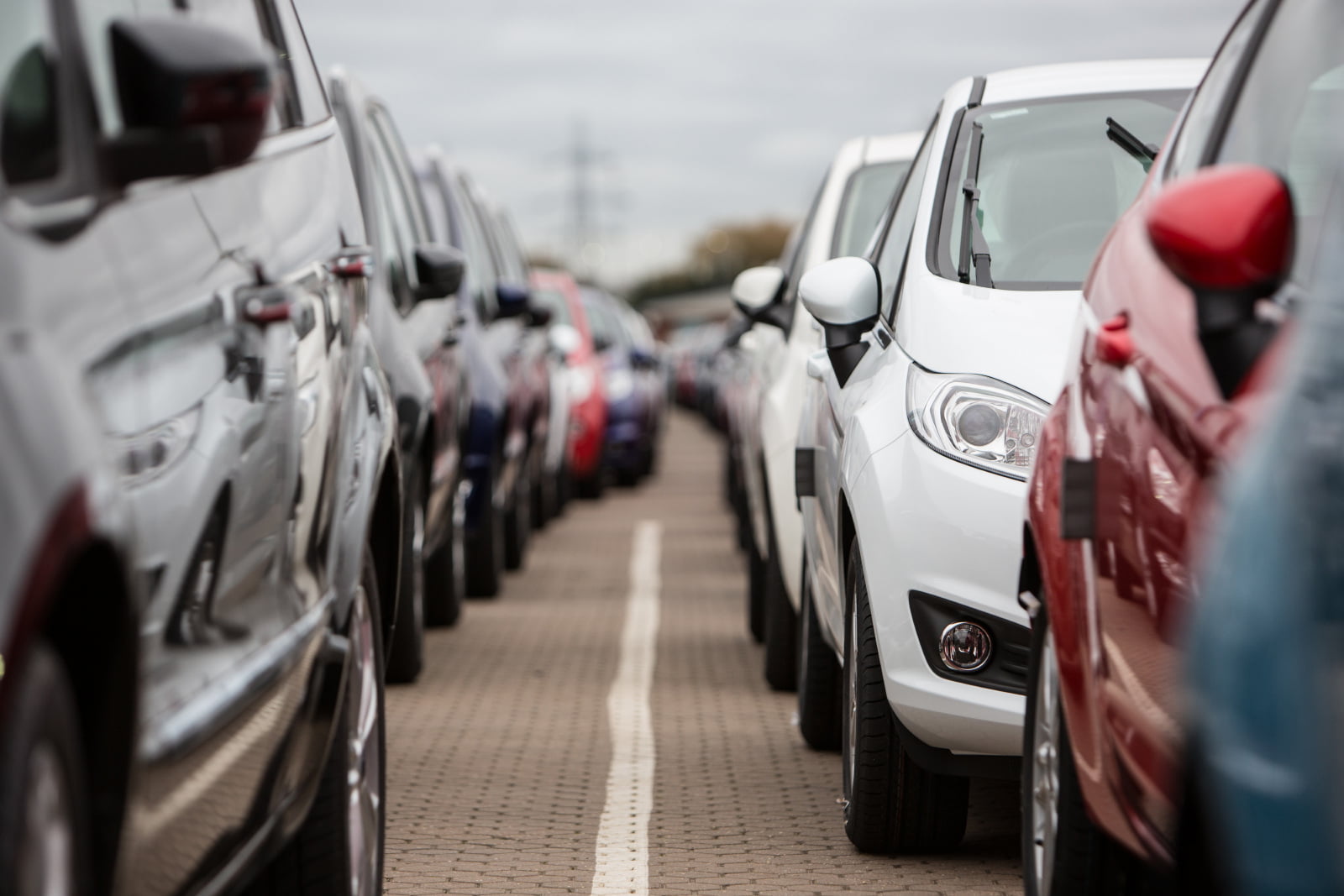
News
Pre registrations
May 2025 new car pre-registration figures
26 Jun 2025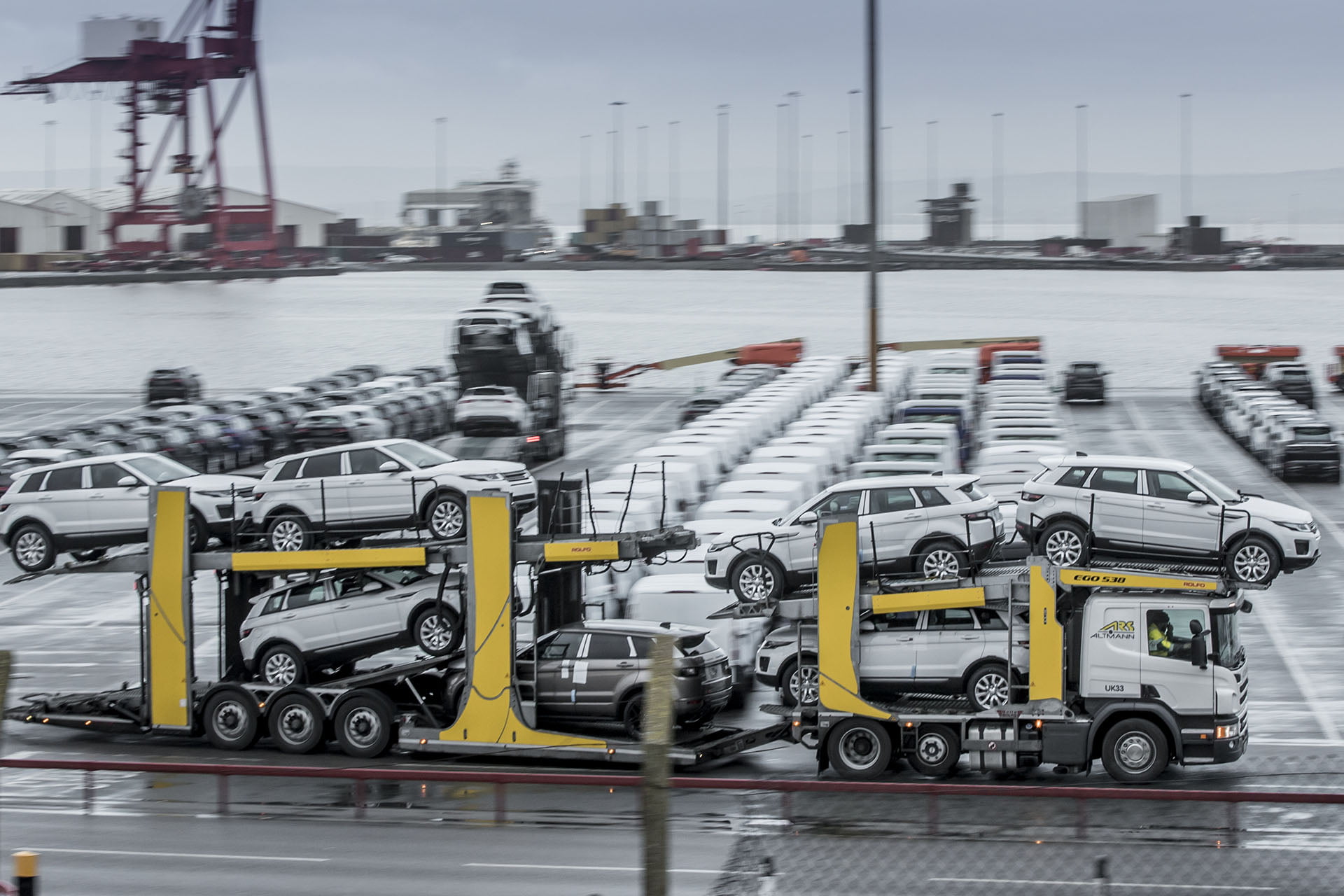
News
Electric vehicle
SMMT response to Government’s Trade Strategy
26 Jun 2025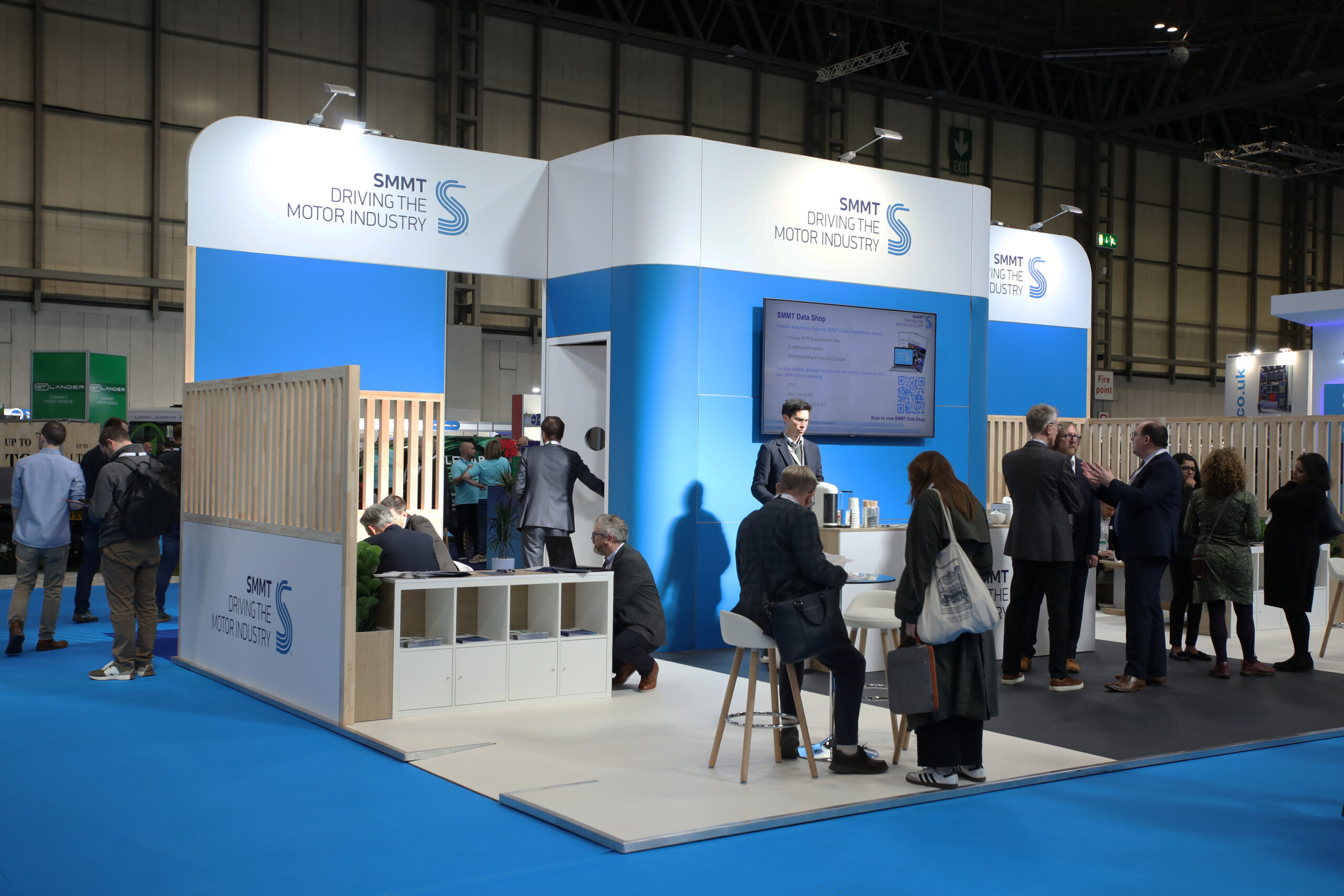
News
Membership