media centre
Keep up to date with the latest news, comment and insight from SMMT, covering all key UK automotive industry issues, developments and trends, including market and manufacturing performance across every sector.
News
FILTER search:
Select year
Select year
2025
2024
2023
2022
2021
2020
2019
2018
2017
2015
2014
2013
2012
2011
2010
2009
2008
2007
2005
2004
2003
2002
2001
2000
1999
1998
1997
1995
1994
1993
1992
1991
1990
1989
1988
1987
1985
1984
1983
1982
1981
1980
1979
1978
1977
Select month
Select month
Jan
Feb
Mar
Apr
May
Jun
Jul
Aug
Sep
Oct
Nov
Dec
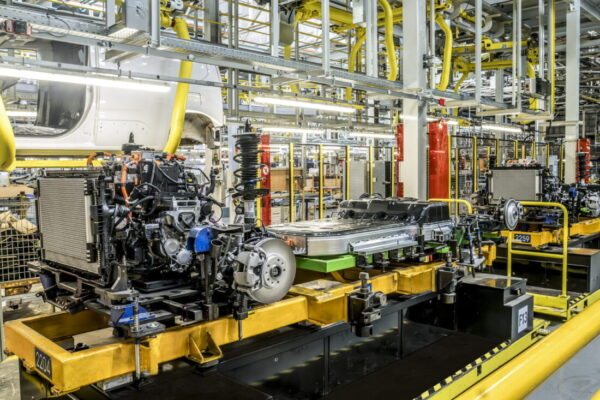
News
Car
Car manufacturing
Vehicle manufacturing growth in March fails to offset first quarter decline
25 Apr 2025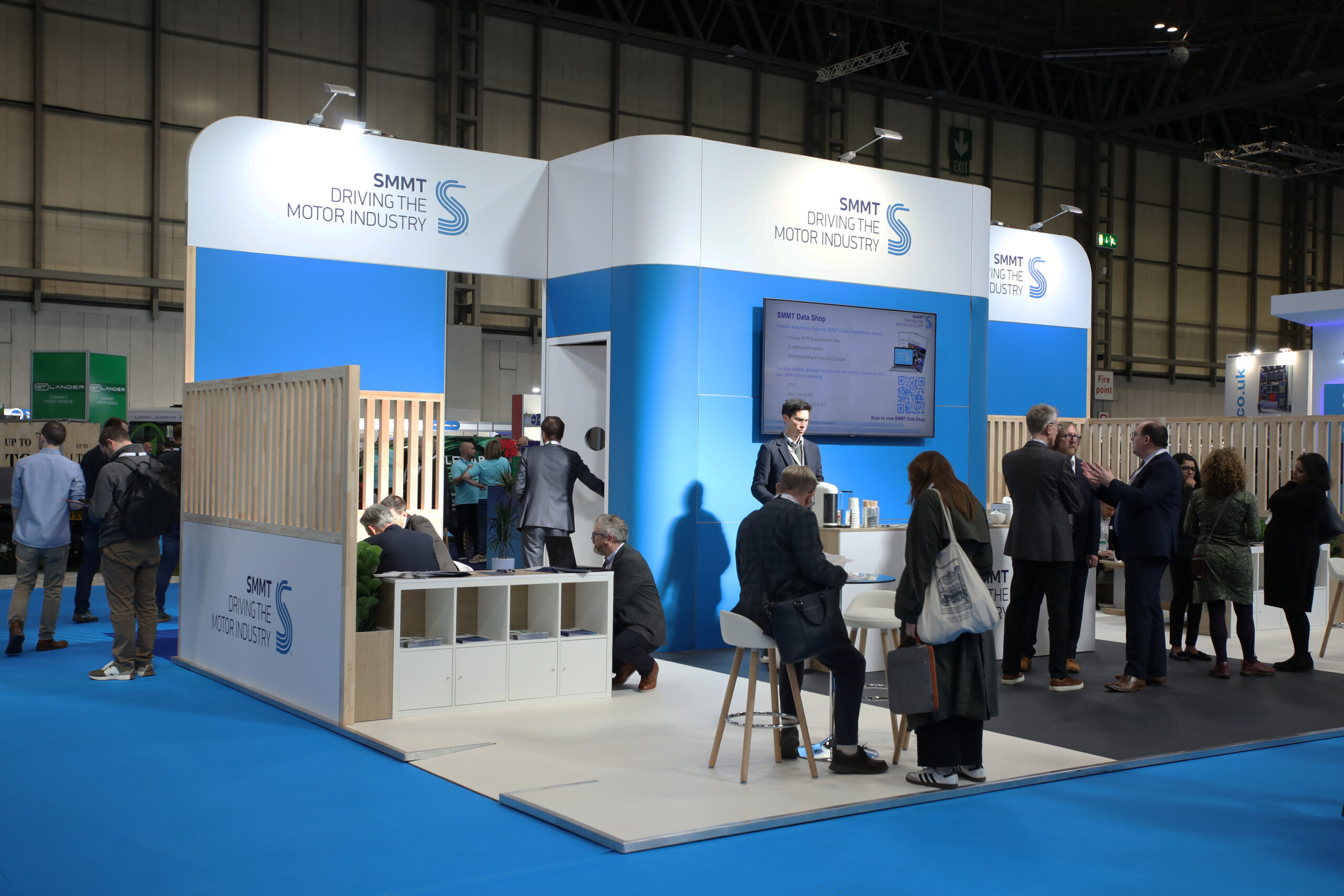
News
Membership
New Members – April
25 Apr 2025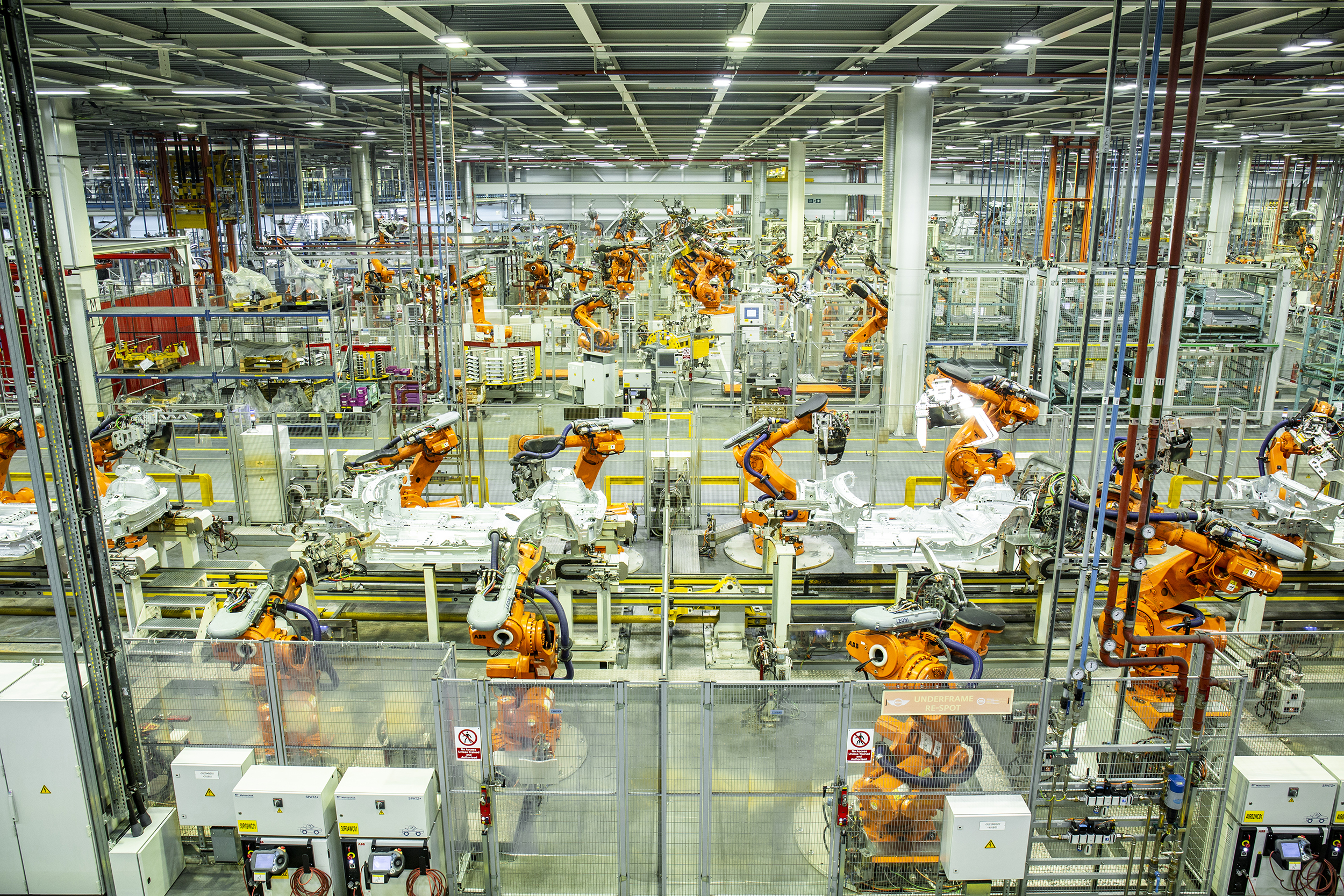
News
CEO Update
Navigate these choppy waters and the sector can drive growth
25 Apr 2025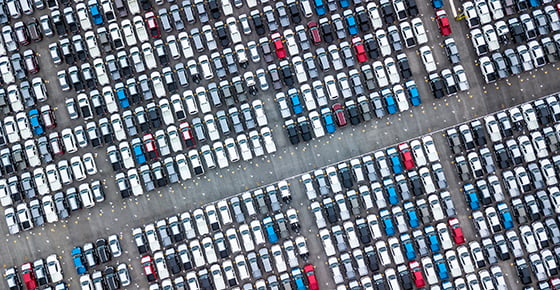
News
CEO Update
A nation of manufacturers – and motorists
17 Apr 2025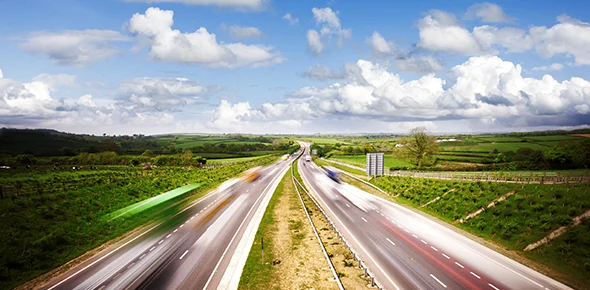
News
Bus & Coach
Bus & Coach registrations
More than a million EVs on UK roads as vehicle ownership reaches new high
12 Apr 2025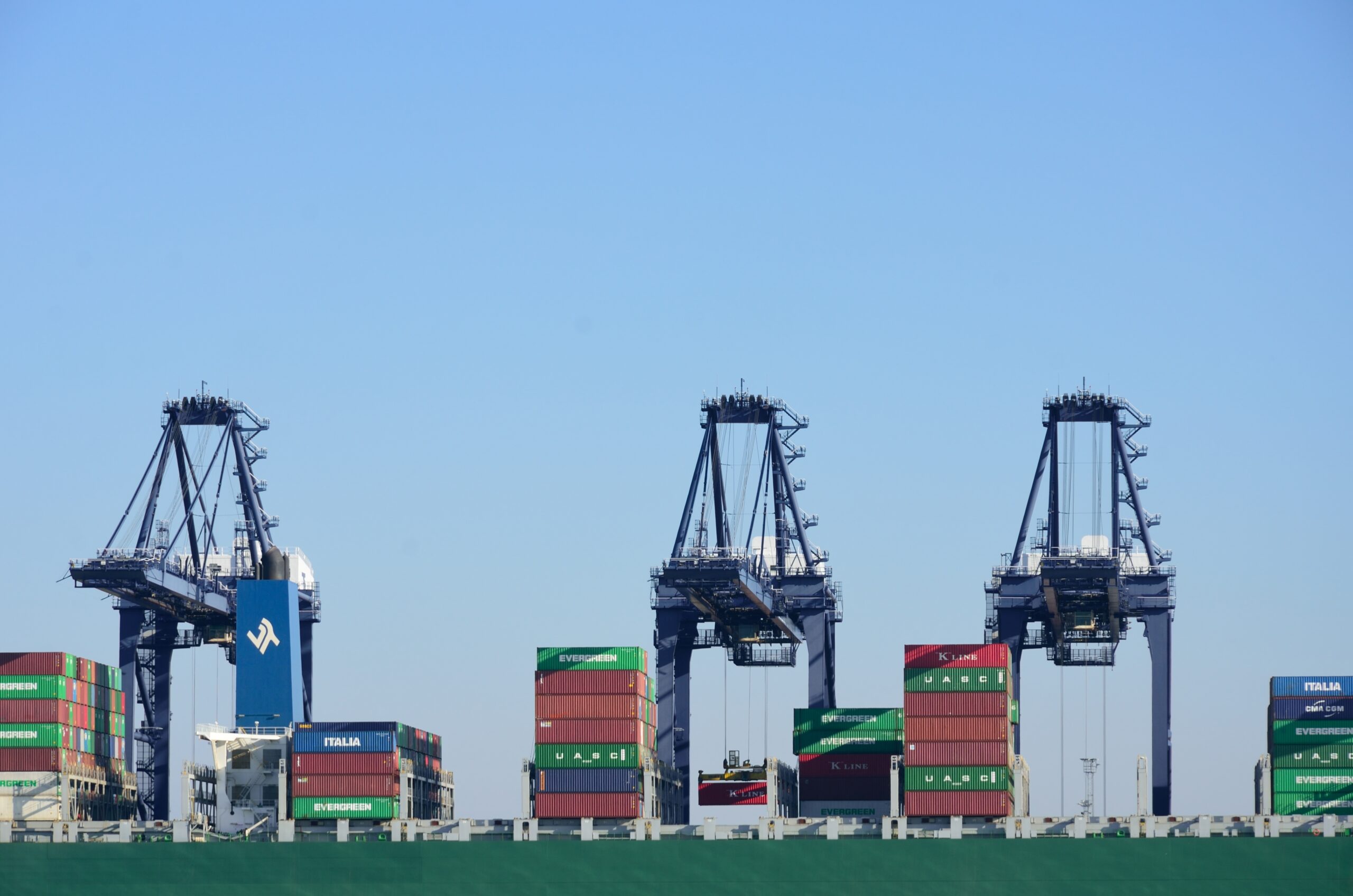
News
CEO Update
A significant first step for UK Automotive
11 Apr 2025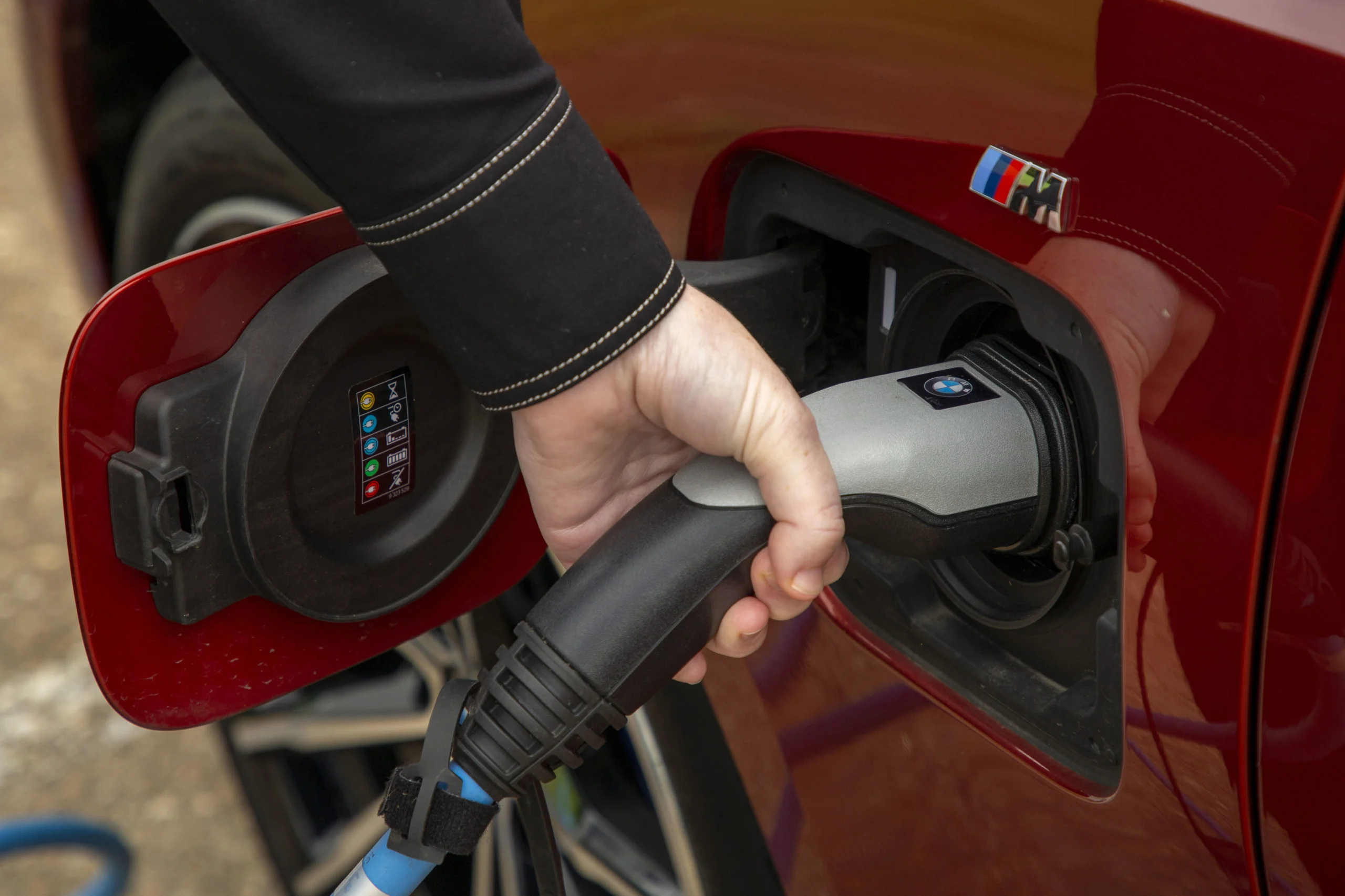
Statements
SMMT statement on changes to Zero Emission Vehicle Mandate
6 Apr 2025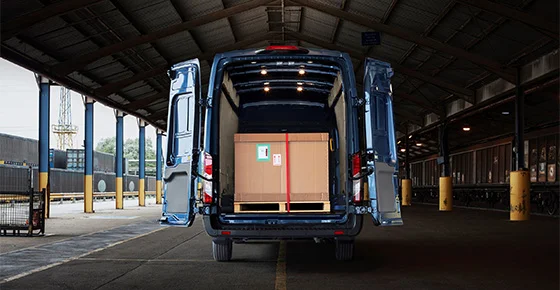
News
Commercial Vehicle
LCV registrations
UK demand for new vans shrinks for fourth month running
4 Apr 2025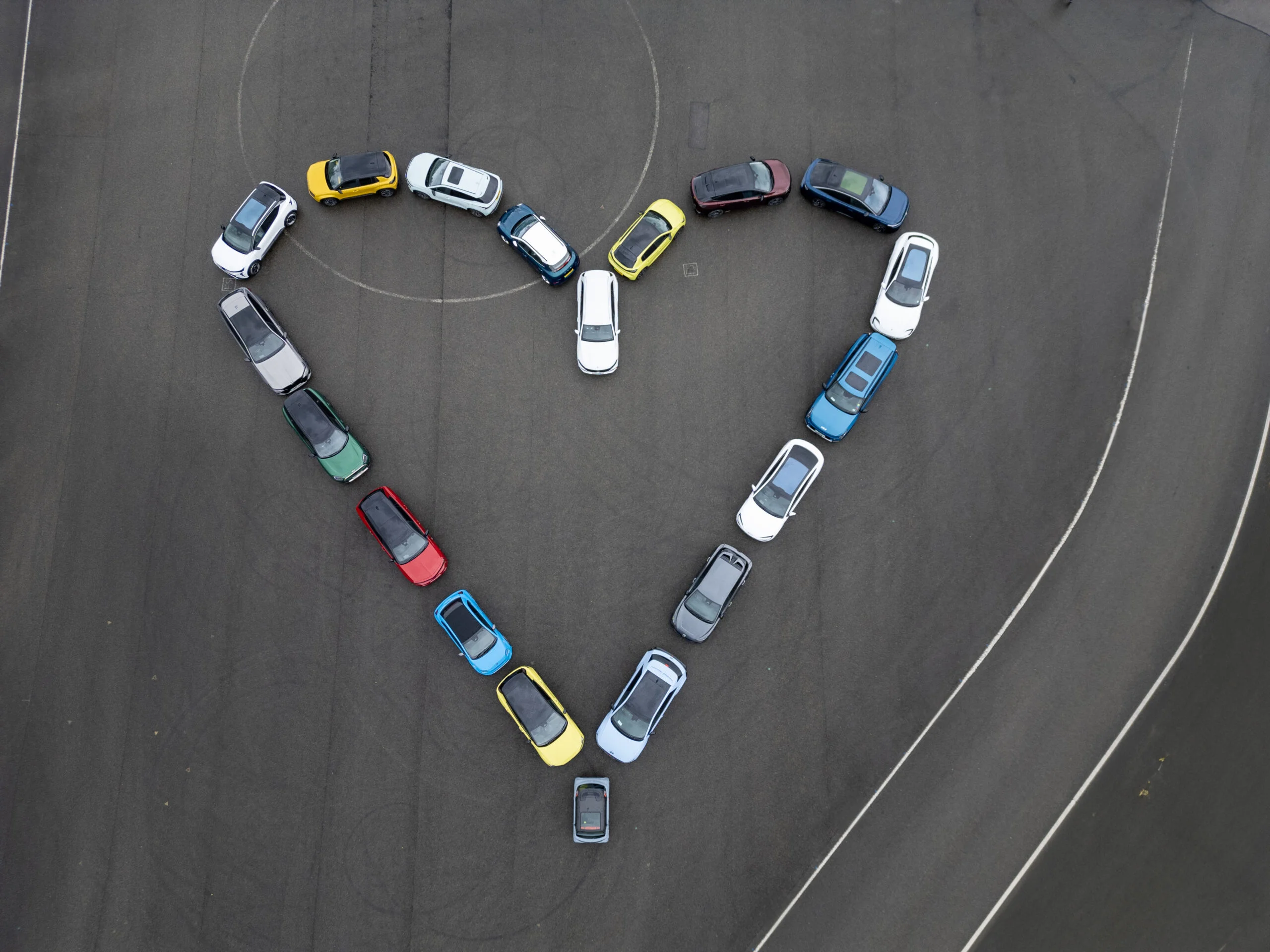
News
Car
Car registrations